for tomorrow.
Our Mission is to provide the traveling public with a safe, cost effective, and unique driving experience across the scenic Chesapeake Bay. That mission never ends and so we're excited to announce the Parallel Thimble Shoal Tunnel Project.
Project Description
The Chesapeake Bay Bridge-Tunnel is a 17.6 mile bridge and tunnel complex that spans the lower Chesapeake Bay and connects Virginia’s Eastern Shore with the mainland in Virginia Beach. The Parallel Thimble Shoal Tunnel project involves the construction of a two-lane bored tunnel from the CBBT’s southernmost island (#1 Island) under Thimble Shoal Channel to #2 Island. When complete, the new tunnel will carry two lanes of traffic southbound and the existing tunnel will carry two lanes of traffic northbound. The new Parallel Thimble Shoal Tunnel will be the first transportation tunnel constructed in the Mid-Atlantic region by a tunnel boring machine (TBM).
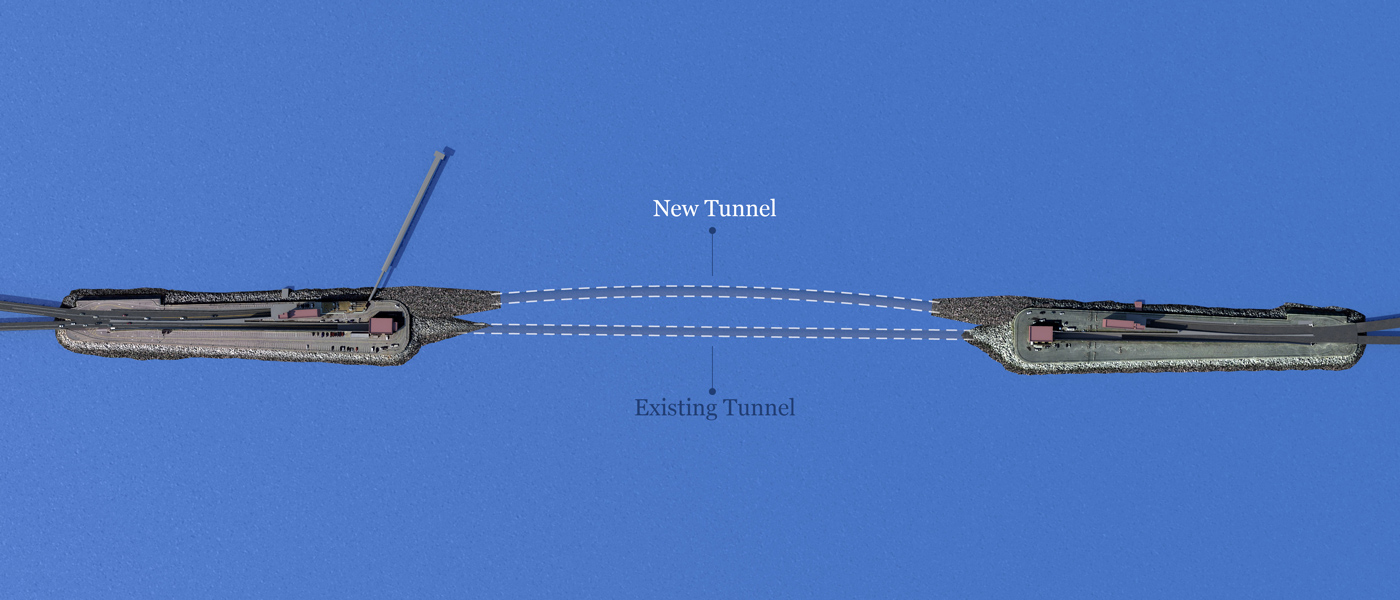
A diagram illustrating the placement of the new tunnel relative to the existing one.

Environmental Approach
The Chesapeake Bay Bridge and Tunnel District and Chesapeake Tunnel Joint Venture are committed to protecting the Chesapeake Bay and minimizing environmental impacts as a result of construction of the Parallel Thimble Shoal Tunnel. The following documents provide information in regard to the environmental approach for this project as it pertains to water quality, the management of construction materials and the minimization of general environmental impacts resulting from project construction.
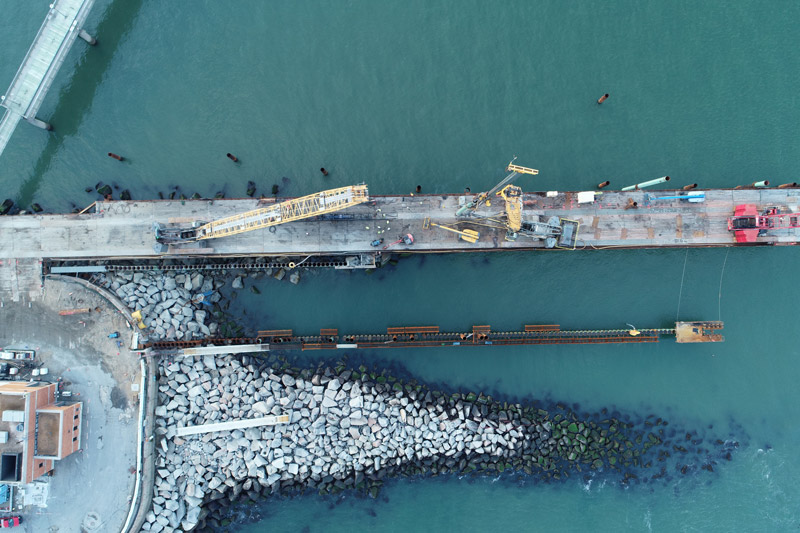
Project Funding
The Parallel Thimble Shoal Tunnel Project will be funded through a variety of means, including 1) the sale of revenue bonds, 2) TIFIA loan, 3) VTIB loan, and 4) monies from the District’s General Fund.
Meet Chessie.
In keeping with tunneling tradition, the CBBT hosted a TBM Naming Contest in the spring of 2018. The contest was opened to area 6th grade students and in April, after public vote, the TBM that will bore the CBBT's parallel tunnel was named CHESSIE.
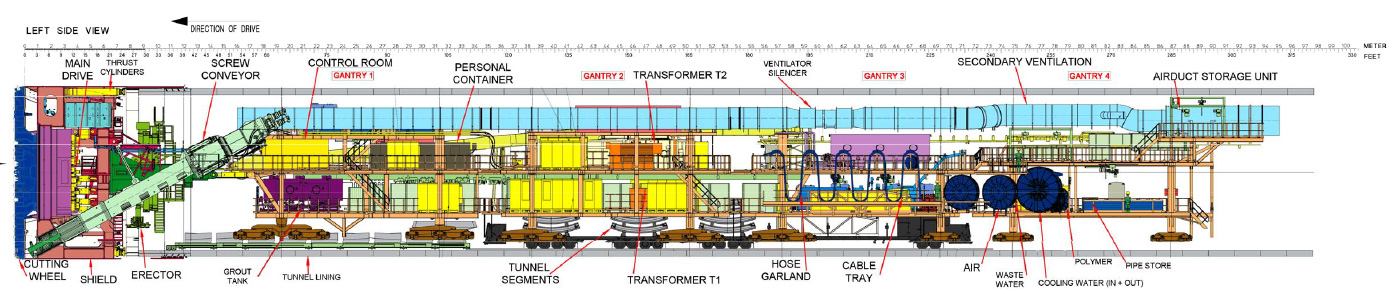

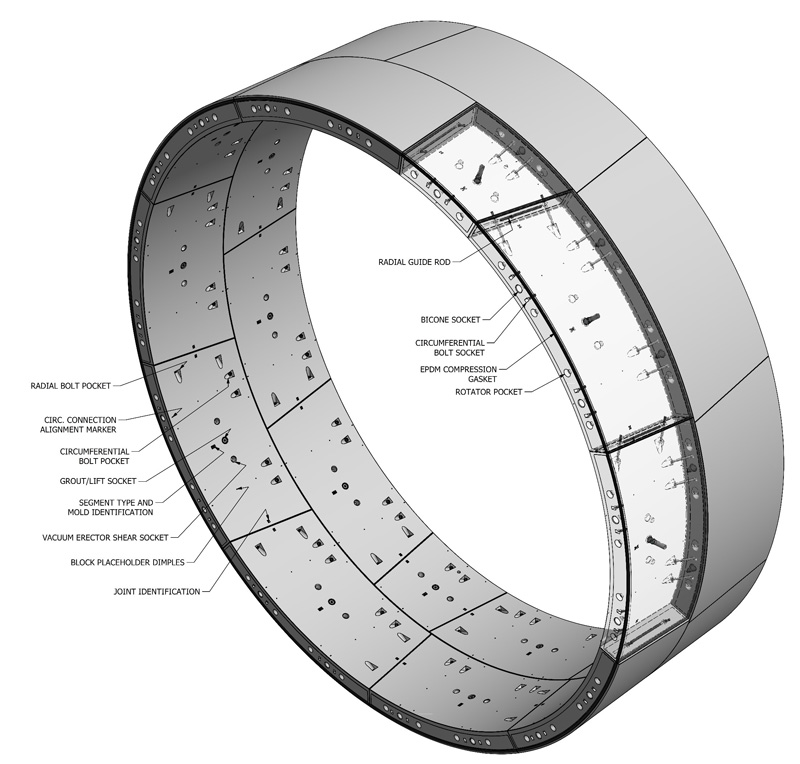
Tunnel Project.
TBM Name
Chessie
TBM Manufacturer
Herrenknecht of Germany
TBM Type
Earth Pressure Balance TBM
Total Weight of the TBM
3,075 US Tons or more than 6 MILLION pounds
Overall Dimensions
308 feet in length
Cutterhead Size
43.5 feet in diameter
Maximum Rotation Speed
2.3 rpm
Maximum Number of Cutting Tools
559 cutting tools, used to remove the soil from the tunnel face.
Geological Conditions
Sand and soft and stiff layers of clay
Power
10 MW (megawatts) or the equivalent of energy to power 2,500 homes
Speed
Slow! Maximum advance rate of 2.4 inches per minute. Will advance approximately 50'-60' per day. It will take approximately one year to complete the tunnel bore.
Tunnel Segments
9,000 total segments; 10 tons each; 5 yards of concrete per segment; 18" thick; Manufactured by CSI of Chesapeake, VA and transported to the job site by truck and then into the tunnel by mining cars.
Tunnel Lining
Comprised of precise, prefabricated segments; ten segments complete one ring.
Erector
A lifting device with a rotating vacuum plate for handling the tunnel segments during the ring build.
Thrust Cylinders
A total of 38 thrust cylinders push the shield away from the tunnel ring that was last installed, advancing Chessie forward.
TBM Entry
Chessie will be lowered into a receiving pit on #1 Island and begin the tunnel drive.
TBM Exit
Chessie will end the tunnel drive on #2 Island.
Soil Removal
Chessie will remove approximately 500,000 cubic yards of soil. All soil will be disposed of at a DEQ-approved landfill.
Crew Size
20-25 people around the clock. There will be two 10-hour shifts with one 4-hour break for maintenance.
Control Room
All data and control systems required for the operation of the TBM are in the control cabin. Machine advance rate, drive direction, cutting wheel speed, and screw conveyor speed can all be adjusted from this room by the TBM Operator.